| 4JET microtech, Around 4JET Lasers Produce Shark Skins on Aircraft
Alsdorf / Hamburg
New Process to Create Riblets debuted at IntAirCoat Conference 2019
During IntAirCoat Conference 2019, Laser specialist 4JET and leading aircraft paint supplier Mankiewicz (Hamburg, Germany) have introduced a new laser process for the creation of fuel saving riblets automatically lasered onto painted aircraft surfaces.
The technology – dubbed LEAF for Laser Enhanced Air Flow – uses the principle of laser interference patterning to quickly create fine lateral grooves in the uppermost layer of aircraft paint.
Such riblets have been proven to reduce drag by up to 10 percent which results in fuel savings for commercial long-haul airlines by more than 1 % – equaling tremendous potential savings on total global kerosene spending of 150 bn US$ annually.
The process – while still in the development stage – already yields industrial throughput levels and has passed initial qualifications for durability.
Working Principle
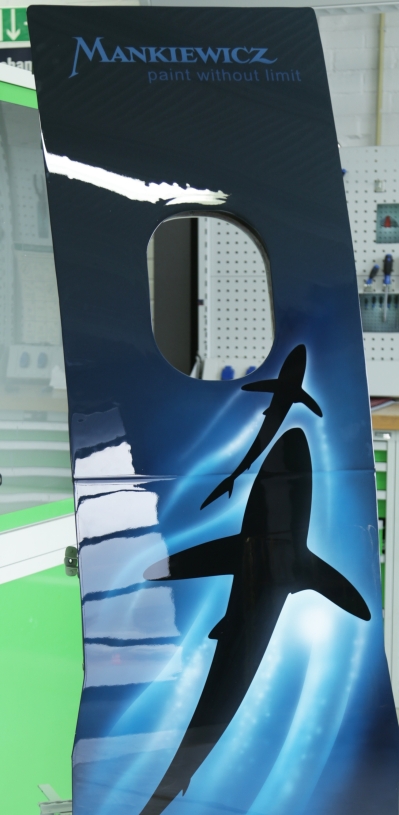
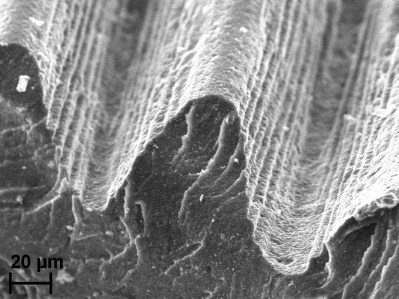
Removing paint by lasers is a well-known technology but so far proved to be too slow to create the high density of riblets required to achieve “shark skin” effects.
Instead of creating the riblet grooves with one focused laser spot “line by line”, 4JET has now found a way to speed up the process by a factor of about 500 using the principle of laser interference patterning:
The laser beam is split up and recombined on the surface in such a way that the electric field oscillations of the light waves superpose in a controlled manner. This superposition creates a distinct pattern of dozens of alternating equidistant lines of high and almost no intensity within one single laser spot. This enables to create 15 kilometers of riblets – equal to about 1 m² of riblet surface – within less than one minute.
And to add even more benefits; LEAF is working dry without any consumables. It allows to adjust riblet geometries depending on their location on the aircraft. The paint dust and vapor created during the process is evacuated and the process does not require post processing. The technology enables to process curved or riveted surfaces and – thanks to its long focal distance – can be integrated with existing robotics used for paint removal or printing operations in aircraft maintenance.
“We are looking forward to actively writing another chapter in the history of aviation coatings and shaping the future of sustainable aircraft. With 4JET we are glad to have such a competent partner of the laser industry at our side and look forward to the future cooperation and commercialization of this ground breaking new method to save fuel and thus contribute to a greener future.“ says Andreas Ossenkopf, Director – Head of Aviation.
4JET CEO Jorg Jetter points out: “We are excited about the progress so far and the tremendous opportunities of our new partnership with Mankiewicz. LEAF could not only be opening up an entirely new market for our company, but deliver a significant contribution to cut down CO2 emissions in the aviation sector.”
About the Cooperation
4JET and Mankiewicz are jointly developing the LEAF technology for use on aircraft and prepare for its commercialization within the next years. Mankiewicz will support the development with its deep understanding of paint chemistry and the requirements of the aviation, while 4JET will focus on the development of the laser process and the riblet forming system.
About Mankiewicz
Mankiewicz is one of Germany’s traditional paint manufacturers, leads the field in the production of both solvent-based and water-dilutable high-tech coating systems for industrial series production. Today, Mankiewicz supplies its high-quality paint products to various different markets such as machine construction, capital goods, automotive, aviation, railway, medical technology and yachts. It is of great importance to us that our products fulfil the demand for highest quality standards. Worldwide more than 1,500 staff members are committed to the realisation of „Coating Concepts of the Future” in accordance with current quality standards. The high quality of the products and processes is guaranteed by a quality management system which was established many years ago. Mankiewicz is certified according to ISO 9001, IATF 16949, EN9100, ISO 14001 and ISO 50001.